Safe, productive outage improves Consumers Energy's Campbell plant
Date Posted: November 29 2019
WEST OLIVE - It was a good, productive 55-day outage that wrapped up this week at the Consumers Energy's J.H. Campbell Generating Facility.
That's the word from Consumers Energy Construction Manager Marty Malek, who expressed satisfaction with the quality, safety and schedule involving the work by building trades union members and their contractors that focused on upgrading the plant's Unit 3."We can't make this happen without the skills and abilities of the building trades," Malek said. "This was a big project for us, and it's apparent going forward that we're going to need a lot more people to come work in the trades."
The outage, which began Oct. 5 employed about 150 tradespeople. This outage focused on efficiency improvements to the newest and largest of the three coal-burning boilers at the Campbell plant: 835-megawatt Unit 3, which first came online in 1980.There are three coal-burning units that comprise the 1,450 megawatt plant, located about 20 miles north of Holland on the Lake Michigan shore. Contractors doing the work for this outage included Northern Boiler, Monarch Welding and Engineering, Newkirk Electric, Southeast Energy and Erickson Crane.
"This outage is about increasing the reliability of Unit 3, and that is part of our promise to the people of Michigan," Malek said.Another promise by Consumers Energy is to reduce and eventually eliminate coal as a fuel. As part of that process, the utility plans to retire the Campbell plant, possibly sometime about 2040. "In the meantime, keeping these units reliable and in good working order is extremely important to us, and that's what we're doing here," said Consumers Energy spokesman Roger Morgenstern.
There were several significant tasks on the to-do list during the outage, and each was supervised by a Consumers Energy project manager. They include: Casey Malotke, Adam Saur, Tim Broilo and Duane Devett. Here's the work they oversaw:Seven-Alpha (7-A) feed water heater equipment replacement. “One of the big challenges we encountered was the rigging in and out of the 161,000-pound vessel,” Malotke said. “The low head room and crowded floor space required a precise and technical rigging plan. The maximum floor loading was also a factor in the removal and replacement project. The craftsmen were able to lay 117 sheets of three-quarter-inch plate steel over the existing grating to build a path through the plant’s second floor. The plate steel created a sealed surface allowing them to utilize air castors to move the feed water heater vessels across the floor to the hoisting bay, where they could use the 100-ton turbine hoist to load out the vessels.”
The result of the heater replacement work will allow the Unit 3 boiler to heat up quicker and more efficiently, and use the same amount of steam to heat a greater amount of water that is recycled back into the boiler.Burner primary airtube replacement. "This was a big project for us," said Saur, who referred to the work as a "longevity upgrade," with the wholesale replacement of system hardware. It included the replacement of all 48 burners on Unit 3.
The last overhaul of this system was in 2007, when the entire works were upgraded to convert to the use of low-sulfur western coal."The trades did an outstanding job, and the safety record has been excellent, too," Saur said. "The schedule is the biggest challenge, but we're helped by having some historical knowledge from the craft to get this done. For example, the rigging is a bit different than in the past, and we made some adjustments. The boilermakers and fitters worked really well together."
Primary air combustion air heaters. Two heat exchangers were replaced as part of the outage, and it was the largest portion of the project, said Broilo. The system heats the primary air that is sent to the boiler's windbox, which supplies combustion air to the burners. They work like an automotive radiator.8.1 onsite bus replacement. Failures of the equipment, and its age, led to the decision to replace the electrical bus on the exterior of Unit 3. "The bus comes off the grid, and is used to provide power to start up Unit 3," said Devett.
He said there are two main electrical buses into the plant, called 8.1 and 8.2. While the plant's output capacity is 1,450 megawatts, the plant itself has its own internal electrical needs - such as power for the post-combustion system - which reduces its output to the grid by about 55 megawatts.The old bus is being removed, while the new bus is going in its place. "We haven't had any surprises," Devett said. "It's just a tough job some days physically loading and getting the bus in and out of the space."
Malek said Unit 3 was slated to come back online on Nov. 28. While Consumers Energy - always a reliable employer of union contractors - was able to get sufficient manpower for this project, there are some caution flags out when it comes to hiring sufficient personnel in the future. The utility has an 88-day outage focused on Unit 1 that's scheduled in February."The benches are empty and the tradespeople are working elsewhere," said Malek. "Plus, the jobs that we have here aren't on a massive scale any more, so we don't necessarily have a readily available workforce. It's a concern going forward."
The unit was expected to return to service Nov. 27, a day ahead of schedule, which Malek said is due to the great collaboration with the trades.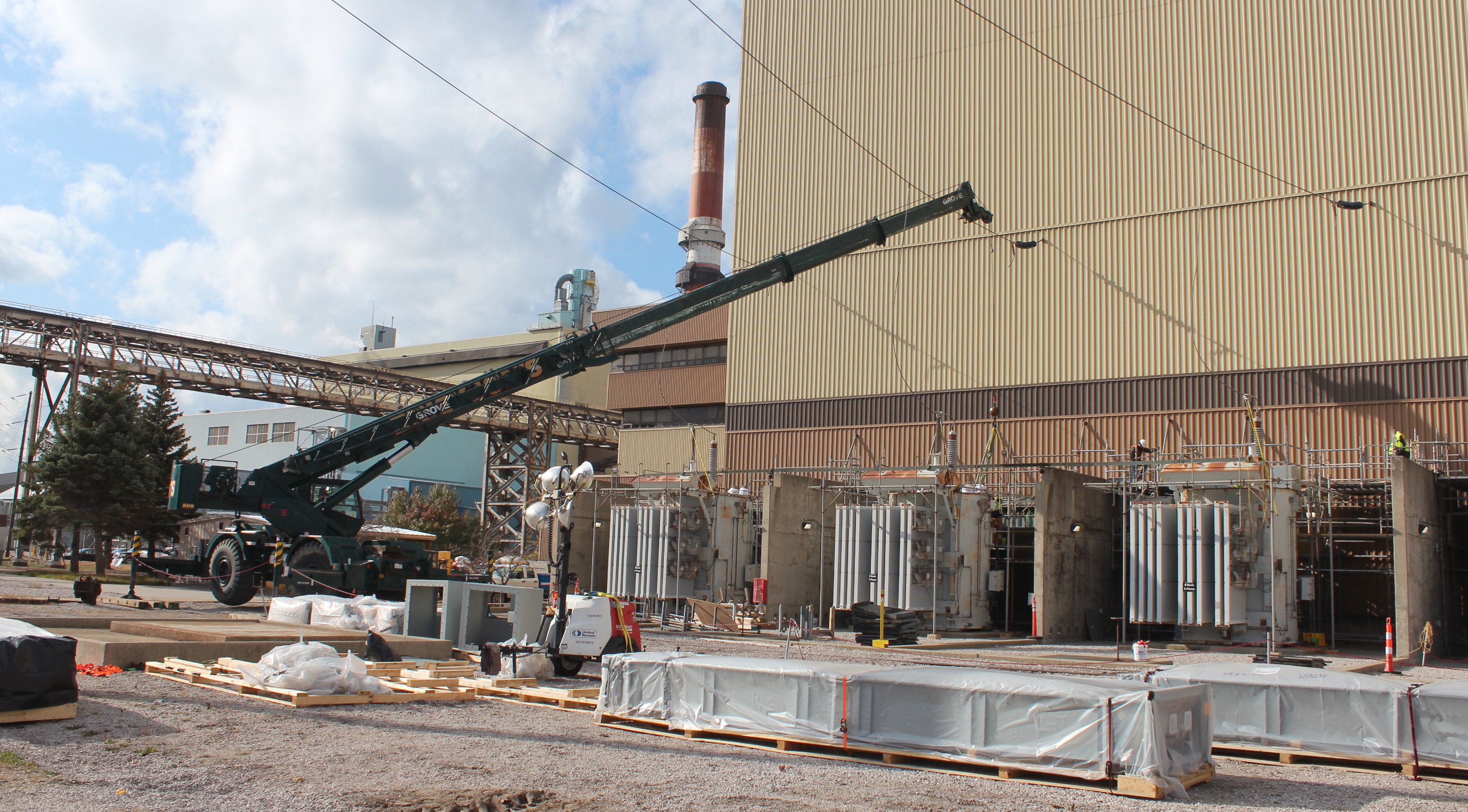
THE 8.1 UNIT 3 bus that was serving Unit 3 at the Consumers Energy Campbell plant in West Olive is being replaced as part of the outage. The new bus, installed on the side of the building by electricians employed by Southeast Energy, is expected to provide more reliable service.
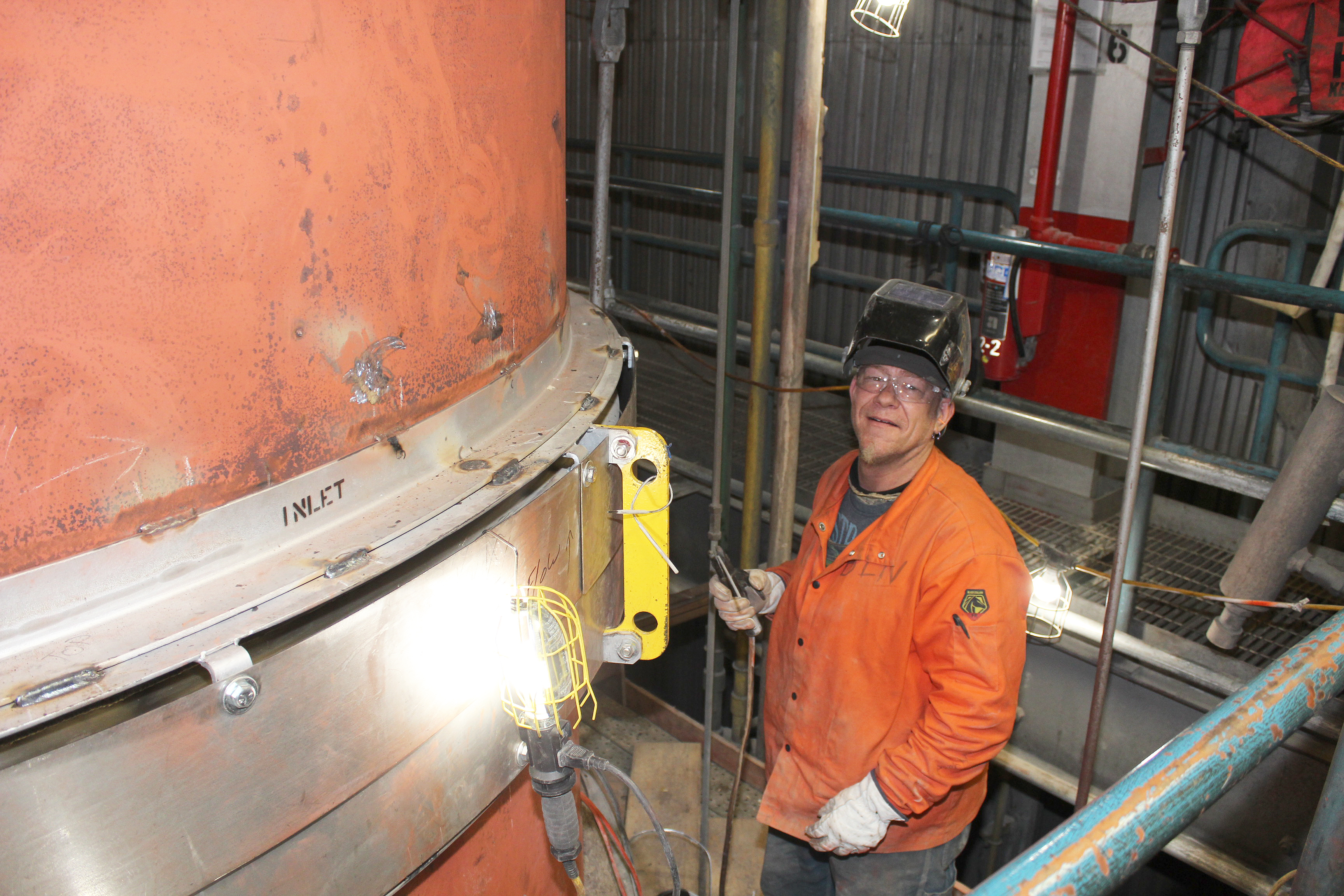
WORKING ON AN EXPANSION joint replacement of an air duct on Unit 3 at the Consumers Energy Campbell Plant is Ben Wilsey of Boilermakers Local 169. He’s employed by Northern Boiler.
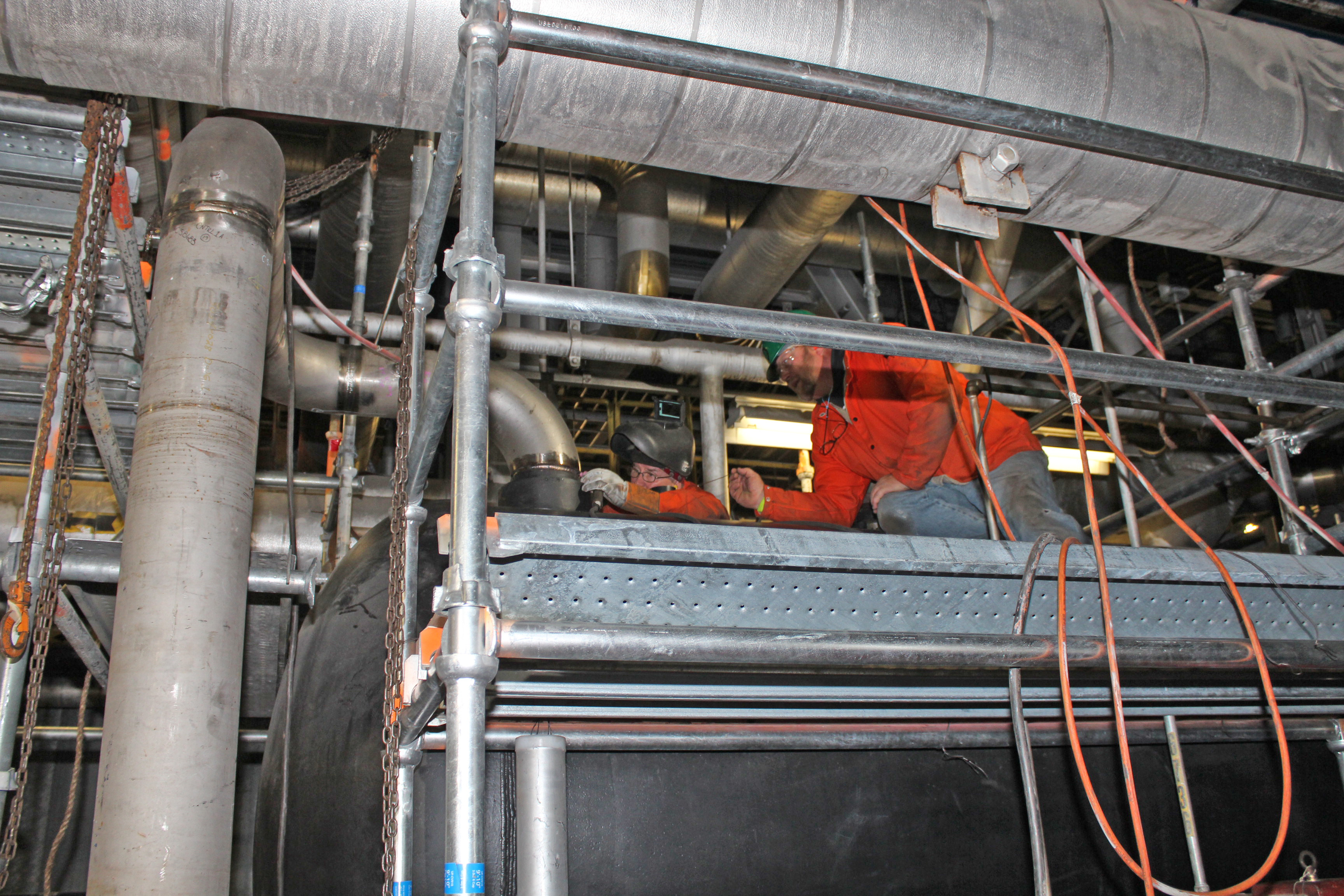
SETTING UP A WELD at feed water heater piping inside Unit 3 during the outage the Consumers Energy J.C. Campbell Plant are Rocky Ferrell and Daniel Harry of West Michigan Plumbers, Fitters and Service Trades Local 174. They’re employed by Northern Boiler.